Biogas / Biomass Pretreatment System
MODEL | NBPS-80 | NBPS-160 | NBPS-250 | NBPS-320 | NBPS-500 | NBPS-800 | NBPS-1800 |
CAPACITY(m³/h) | 80 | 160 | 250 | 320 | 500 | 800 | 1800 |
POWER RANGE(kW) | 30-50 | 60-100 | 120-150 | 160-200 | 210-300 | 320-500 | 600-1000 |
PIPE SIZE | ND50 | ND65 | ND80 | ND80 | ND100 | ND125 | ND150 |
Dry Desulfurization Principle
--- Desulfurization tank: The biogas passes through the packing layer in the tank at one end. After hydrogen sulfide (H2S) oxidizes to sulfur or sulfur oxide that they're left in the packing layer. After purification, the gas is discharged from the other end of the tank.
--- Dehydration tank: The dehydrating tank has a dehydrating ball. When the gas passes through the dehydrating ball, the water is left.
--- Water sealing tank: Fireproof medium is set between the two sides of the firedamp inlet and outlet. When either side catches fire, the flame propagation is blocked and will not burn to the other side.
Dry desulfurization is a simple, efficient, and relatively low-cost desulfurization method. It is generally suitable for desulfurization of biogas with a small amount of biogas and low hydrogen sulfide concentration. The basic principle of the equipment for dry removal of hydrogen sulfide (H2S) from biogas gas is a method in which O2 oxidizes H2S to sulfur or sulfur oxides, which can also be called dry oxidation. The composition of the dry process equipment is to put filler in a container, and the filler layer includes activated carbon, iron oxide, etc. The gas passes through the packing layer in the container at a low flow rate. After hydrogen sulfide (H2S) is oxidized to sulfur or sulfur oxides, it remains in the packing layer. After purification, the gas is discharged from the other end of the container.
Dry desulfurization mainly includes components such as the main steel structure, desulfurizer filler, observation window, pressure gauge, and temperature gauge. The desulfurization tower is usually designed to use one for one, alternate use, that is, one for desulfurization and one for regeneration. The biogas containing hydrogen sulfide (H2S) enters the bottom of the desulfurization tower. In the process of passing through the desulfurization packing layer to the top, the H2S and the desulfurizing agent undergo the following chemical reactions:
Step 1: Fe2O3 · H2O + 3 H2S = Fe2S3 + 4 H2O (Desulfurization)
Step 2: Fe2S3 + 3/2 O2 + 3 H2O = Fe2O3 · H2O + 2 H2O + 3 S (regeneration)
The biogas containing hydrogen sulfide first reacts with the desulfurizing agent with relatively high load at the bottom entrance. The upper part of the reactor is a layer of desulfurizing agent with low load. With a well-designed biogas space velocity and linear velocity, dry desulfurization can achieve a good fine desulfurization effect. .
Before the biogas enters the dry desulfurization tower, a condensate tank or biogas particle filter should be installed. The device can eliminate the particulate impurities contained in the biogas, and make the biogas contain a certain humidity before entering the desulfurization.
When the discoloration of the desulfurizer is observed, or the system pressure loss is too large, another desulfurization tower should be used alternately. The current desulfurization tower undergoes natural ventilation after the biogas is vented to regenerate the desulfurizer. When the regeneration effect is not good, the waste desulfurization agent should be removed from the bottom of the tower body, and the same volume of fresh desulfurization filler should be added to the reactor while the waste filler is discharged at the bottom.
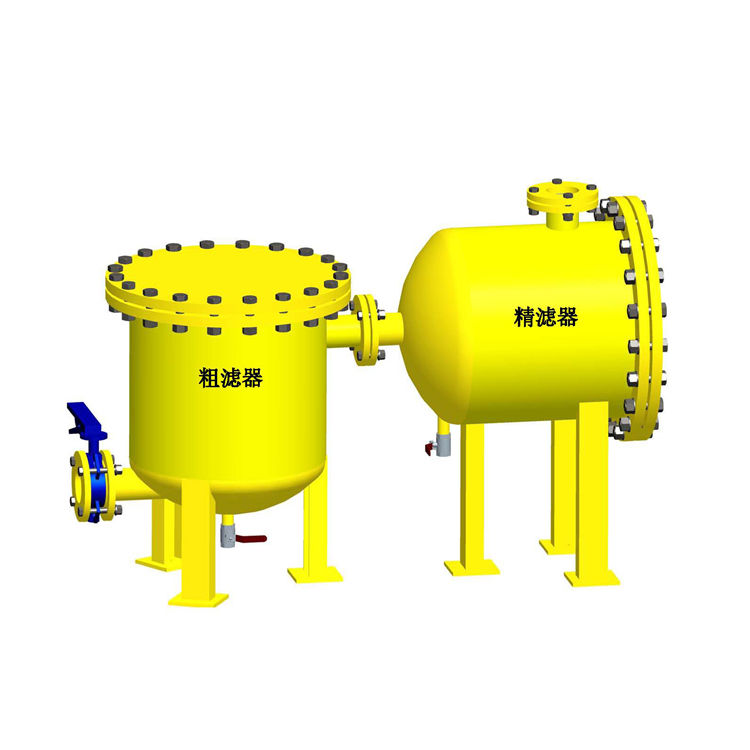
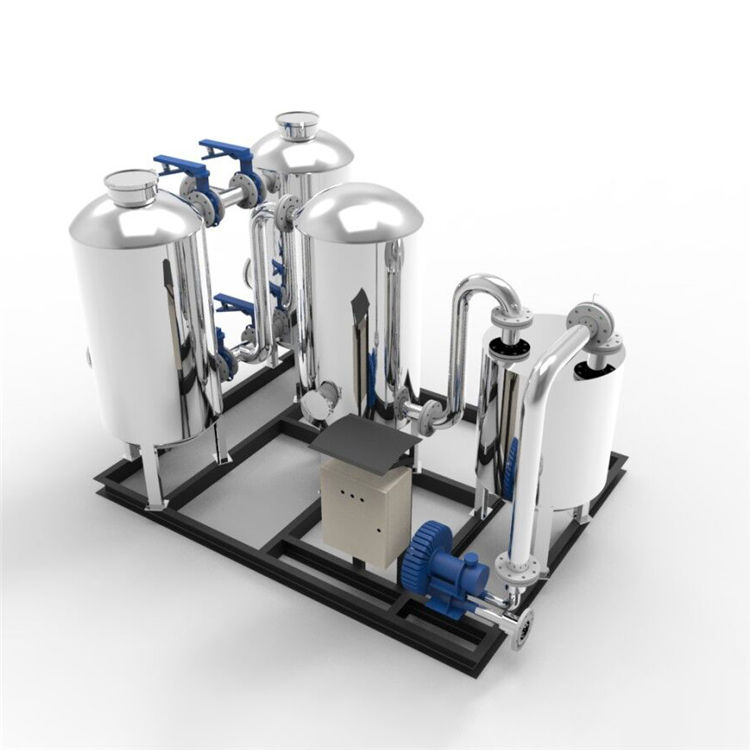
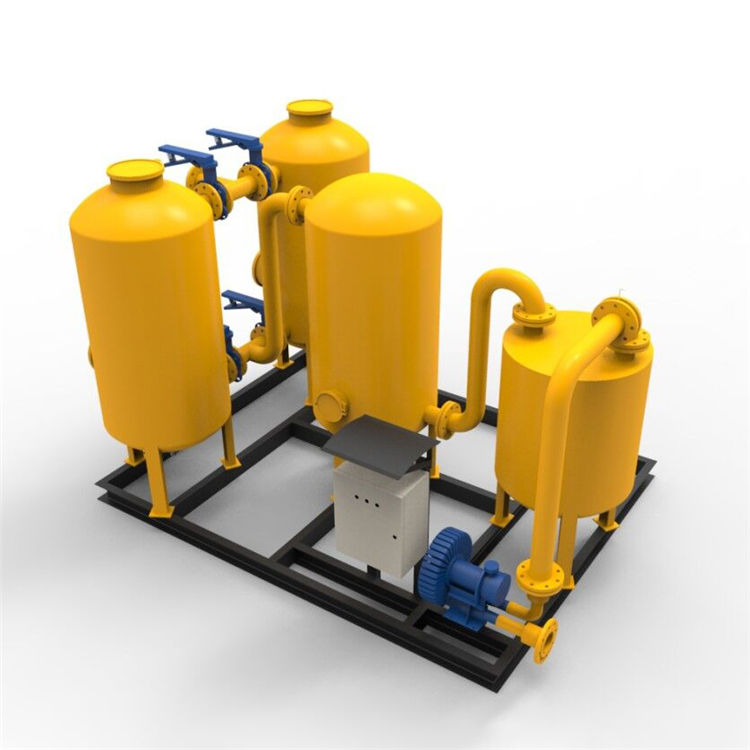